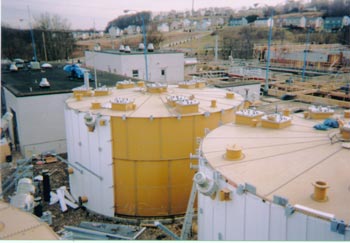
31 Jul Understanding the Different Techniques for Tank Insulation Installation
Explore the technicalities of tank insulation and how Thermacon’s expertise guarantees optimal performance and protection for your tanks.
What is Tank Insulation and Why is it Important?
Tank insulation can aid in the control of heat transfer, either by preventing the excessive loss of heat from the contents within the tank or by restricting the influence of external temperatures on the materials stored within. This is especially important in the petrochemical industry, food and beverage processing plants, and any sector where high-temperature variations can affect stored substances’ quality, safety, and integrity.
The insulation method can be varied based on the tank type and the material stored within it. Common types of insulation include mineral wool, fibreglass, foam glass, and polyurethane foam. Each type of insulation material possesses different properties, such as thermal conductivity, moisture resistance, and fire resistance, making them more or less suitable for certain applications.
High-grade insulation is essential in situations where substances must be kept at a fixed temperature range, such as in the storage of liquefied natural gas (LNG) or other volatile substances. In such scenarios, insufficient or improper insulation can lead to drastic energy losses, thus increasing operational costs.
Panel Installation Technique
A popular method for tank insulation is the panel installation technique. This process involves attaching pre-fabricated insulation panels to the exterior of the tank. The panels, often made of durable materials like polyisocyanurate or mineral wool, are designed to resist weather and mechanical damage while providing superior insulation. This method allows for a fast and efficient installation process and easy access for future inspections or repairs.
Spray Foam Insulation Technique
Spray foam insulation is another commonly employed method. This involves the application of a sprayable foam directly onto the tank’s surface. As the foam expands, it fills gaps and creates a seamless insulation layer. This method is especially effective for irregularly shaped or hard-to-reach areas. It offers excellent thermal performance and prevents moisture ingress, though it typically requires professional handling due to the complexity of application.
Insulation with Protective Coating
For additional durability, some tank installations involve an outer protective coating over the insulation layer. Materials such as aluminum or stainless steel can provide a weather-resistant shield, safeguarding the insulation against environmental factors and mechanical impact. This method enhances the insulation’s lifespan, reduces maintenance needs, and ensures the tank’s integrity over time.
The Thermacon Advantage
At Thermacon, we pride ourselves on our technical knowledge, commitment to safety, and exceptional service. We carefully evaluate each project to determine the most appropriate insulation technique, considering factors like tank size, shape, operational temperature, and environmental conditions. Our team of skilled professionals ensures a high standard of installation, offering an effective, long-term solution for your tank insulation needs.
Final Thoughts
Understanding the different installation techniques for tank insulation can help you appreciate the intricacies of the process and make informed decisions about your insulation needs. Regardless of the chosen method, the goal remains the same: to provide a secure, efficient, and durable insulation solution for your tanks. Trust Thermacon’s expertise to guide you through this process, delivering insulation performance that truly stands the test of time.
Sorry, the comment form is closed at this time.